At first glance it doesn’t look like much, a flat piece of black licorice, perhaps. But the superlight KONE UltraRope® is a completely new take on elevator hoisting. Made of a carbon fiber core surrounded by a unique high-friction coating, it weighs only about a fifth of a similar conventional steel rope.
You might not think about it, but the weight of an elevator’s ropes impacts everything. The lighter the rope, the smaller and lighter the elevator counterweight and sling. So, a lighter rope reduces the overall moving mass and energy consumption significantly. This matters, especially as buildings are getting taller. The top ten tallest in the world each already reach heights of more than 500 meters, or roughly 100 floors per building. In structures this tall, using conventional elevator hoisting technology means moving masses weighing around 27,000 kilograms. This is like fitting ten off-road vehicles inside the shaft and moving them up and down alongside the elevator!
At around this point the ropes become so heavy that additional ropes are needed just to hoist the weight of the ropes themselves. This is one reason most very tall buildings feature sky lobbies reachable from ground floor by one set of elevators, with another set of elevators taking people onwards to higher levels.
Enter KONE UltraRope.
It cuts the weight of moving masses inside the shaft for a 500-meter-tall building to roughly 13,000 kilograms, or the equivalent of 4 off-road vehicles. This reduction is so significant that it enables travel from ground floor to penthouse in one continuous elevator journey – even in a building that rises to a height of one kilometer!
"With a hoisting rope that is 80% lighter than conventional steel rope, we achieve a 15% reduction in energy consumption for our high-rise elevators. This not only translates to enhanced operational efficiency, but also leads to 11% decrease in the overall lifecycle carbon footprint,” says Timo Vlasov, head of MP offering at KONE.
Less deadweight, more benefits
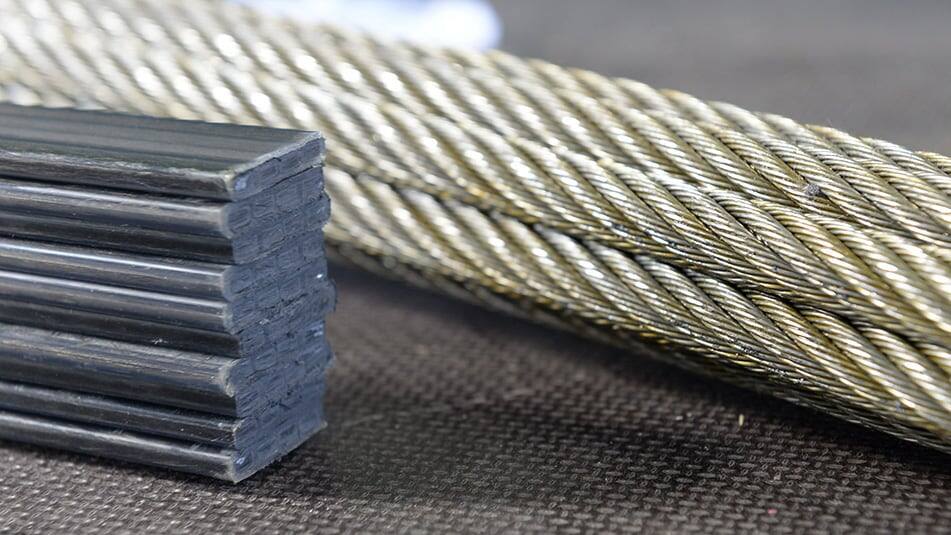
With KONE UltraRope, the higher you go, the bigger the benefits because the lower moving masses enable cuts in the deadweight that’s transported up or down every time someone hops into a high-rise elevator. This means less energy consumption and lower operating costs. For example, the energy savings for a 500-meter elevator journey using KONE UltraRope is around 15% when compared to conventional technology. For an 800-meter journey, the savings are over 40%.
Building sway is another challenge faced by elevators in tall buildings. Here, again, KONE UltraRope offers a solution. Because carbon fiber resonates at a completely different frequency to most building materials, including steel and concrete, KONE UltraRope is less sensitive to building sway and enables reductions in elevator downtime during strong winds and storms.
The Marina Bay Sands integrated luxury resort in Singapore was the first to replace some of its conventional steel ropes with KONE UltraRope. Other major projects like Sky Tower in Auckland, New Zealand, the premium 180 Brisbane office building in Australia, and the 57-story 110 North Wacker in Chicago have also adopted the new technology.
No rust, no wear
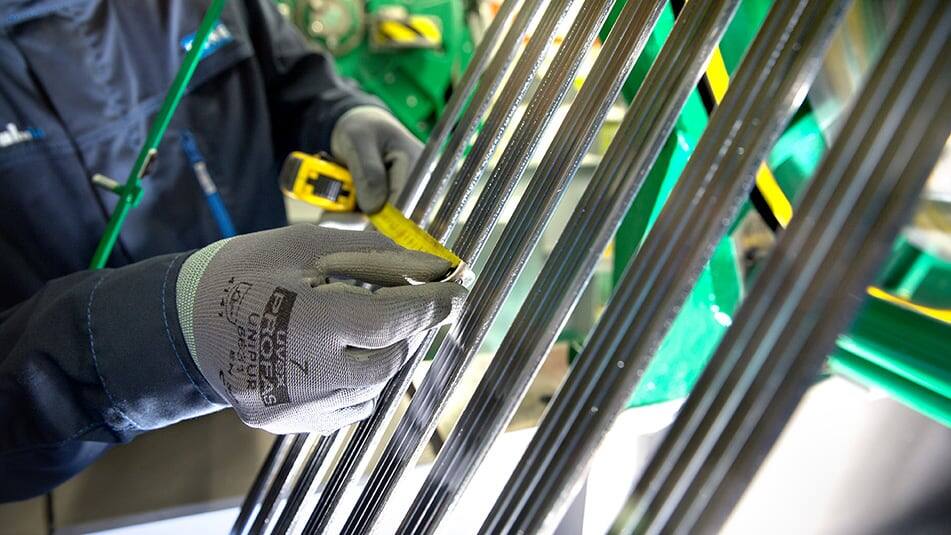
While KONE UltraRope makes travel easy, it also makes maintenance hassle-free. Unlike steel, it does not rust, stretch, or wear. Its special coating does not require lubrication, making environmentally friendly maintenance the status quo.
KONE UltraRope’s longer product lifetime is a boon too, as changing ropes in a tall building is no easy task.
“Today, KONE UltraRope is more relevant than ever,” Vlasov says, “and it greatly contributes to our sustainable success with customers strategy.”